Pallet Palace
Green Building & Purchasing
Welcome to the Pallet Palace 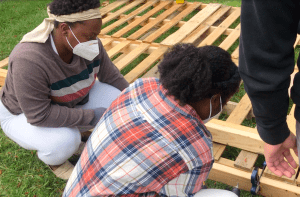
Exciting things are happening in the realm of sustainability projects for the built environment this quarter. A team of students is working towards the goal of framing a unique type of modular tiny home as a creative space. In keeping with our mission of incorporating reclaimed materials into the build, we are framing the house largely out of pallets. While this has been done before in varying capacities (often small structures like sheds), our approach will allow for high ceilings and a large ratio of living area to wall material. Building this structure in the age-old style of an A-frame will ensure rigidity given the use of reclaimed materials, while allowing for a creative use of space, including a sleeping loft on the second floor.
Updates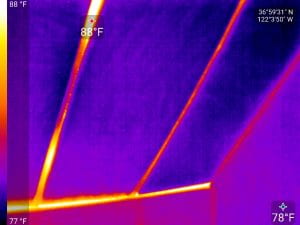
This year, the student team have been taking a closer look at innovations with building insulation. Springboarding off the idea of using discarded wood pallets to frame a house started last year, students have been motivated to incorporate trash items into wall insulation. The most ideal material we are looking into is discarded styrofoam, since it already exhibits great insulating qualities with no further processing. This, coupled with the recent announcement that the Santa Cruz resource management center Grey Bears can no longer accept plastic foam from UCSC, has driven our endeavors forward. For our purposes, foam of mixed polymer types is no problem since there is no chemical processing we need to do. This has the potential to find use for a large amount of currently unrecyclable, or at least unfeasible to recycle, plastic waste.
To make an effective product, students are testing different options of material in which to embed foam scraps, in order to completely fill a wall cavity, to achieve a high R-value. One leading option we have explored is aircrete, which is cement mixed with dense foam which hardens to a low density, porous block upon curing. Testing of different mixing ratios and procedures is underway to establish the feasibility of this option. Another option we are investigating is the use of conventional polyurethane foam, the same type typically used in spray foam insulation. Filling with used styrofoam first would drastically reduce the new amount needed to obtain a desired R-value. We have developed a standard operating procedure for mixing this aircrete and tested the different ratios for thermal insulating properties using a thermal imaging camera. Thermal imaging is our best option for doing this currently, as more rigorous R-value tests require expensive equipment and a controlled lab environment.
After a long hiatus due to remote instruction, students have learned how to properly and safely use the tools required for such a build, as well as some of the basics of conventional framing so that they know what they need to replicate using pallets. Students shown in the photographs can be seen assembling six pallets into what we are calling a “slab”, with full length lumber in between. Putting a selected number of these slabs side by side forms the bulk of the house. Our preliminary work here is to investigate the best fastening methods, as well as gain an understanding of what slab size will be manageable for modular construction. As with many IDEASS projects, this one is completely led by students, with mentoring and guidance provided by the instructor. In this unique setting, we never quite know exactly what the end product will be. For students continuing this project in the Fall, there will be opportunities for discovering/developing other reclaimed and/or low impact materials to be used for roofing, siding, and insulation.
Be on the lookout for events in the coming quarters where students will demonstrate the assembly process of this house.